Applications that help improve your business value chain
Manufacturing drawings and documentation
As would be expected, CAE systems invariably produce detailed mechanical and electrical drawings for control panels, but they can also do much more by, for example, automatically generating terminal schedules, bills of material (BOMs), PLC I/O allocation tables and other essential items of documentation. Automating the creation of manufacturing drawings and documentation through CAE can relieve design engineers of much tedious work. And, as an added benefit, documentation created by a CAE system is guaranteed to be accurate and complete.
Preparing the cabinet and mounting plates
Metalworking operations in the panel building sector, which include drilling mounting plates and making cut-outs in cabinets, have traditionally been carried out manually, using hand tools. For low-volume production, this approach can still be effective, but even then, the use of a CAE design system offers substantial benefits, as full-size drilling templates can be produced and printed with ease. Temporarily attached to the mounting plate or cabinet face that is being drilled or cut, they make accuracy easy to achieve and greatly reduce the opportunity for mistakes.
Even bigger benefits accrue from embracing automation. CNC machines are available that will take data directly from the CAE system and use it to make cut-outs in any type of sheet metal work. With a seamless data transfer between engineering and production, errors and scrap can be eliminated, and panel processing times can be improved by up to 89%.
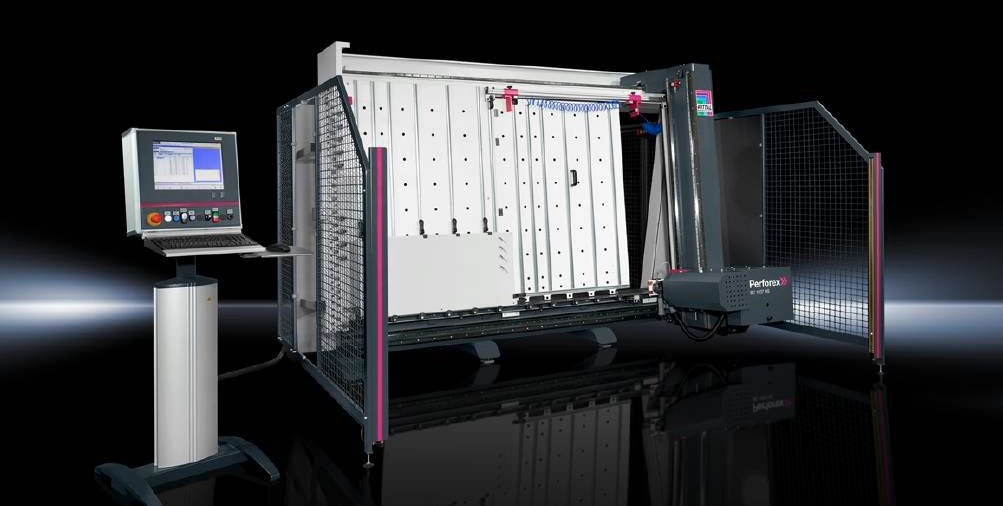
CNC machine by Rittal, Rittal Perforex BC.
Terminal rail assembly
Assembling terminal rails for panels can be a very tedious task, however, there is an excellent alternative: let the terminal supplier build your terminal rails for you.
A modern CAE system can help prepare terminal rail information, including details of spacers, barriers and marker legends, in a format that can be transmitted directly to the terminal supplier who will then provide fully assembled rails ready for use. This system can be used effectively to save time and money.
Wiring
Wiring is yet another time-consuming job that can be simplified through the use of a good CAE system. First of all, a 3D design package will make it easy for the design engineers to preview all of the wiring runs within the panel and to decide on the best routes that will provide optimum segregation between, for example, power and signal cables. The package will also calculate the exact length of each wire, generate the information needed to produce cable markers, and export said data to wire and cable marking machines. If required, it will also produce a point-to-point wiring diagram that includes the size, insulation type, colour and type of every cable in the panel. This greatly speeds the wiring process and reduces the risk of mistakes. In addition, interfaces exist between CAE software and fully automated wire processing machines to deliver an eight-fold acceleration in wiring processing speed.
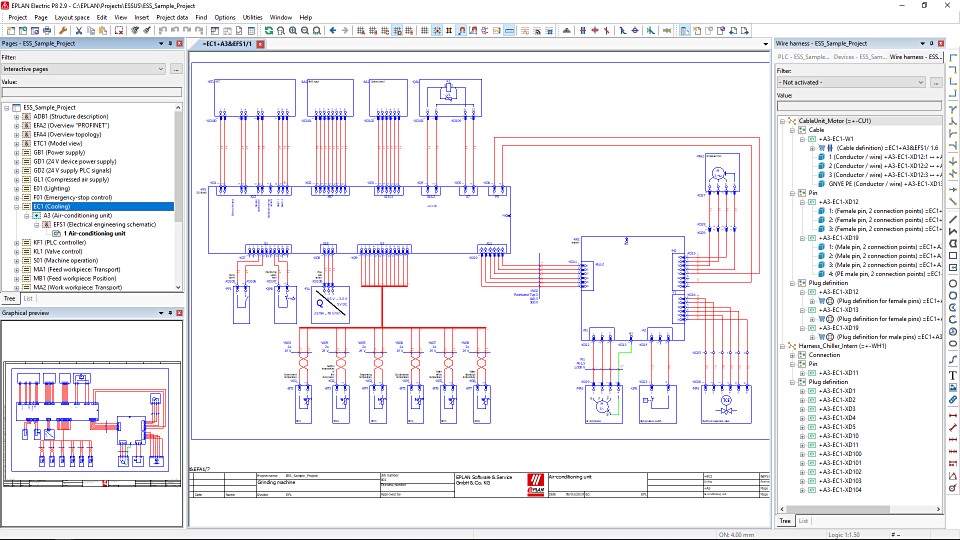
Wiring diagram in EPLAN Electric P8.
Testing
After the panel has been built, it needs to be tested, and keeping the time spent on testing to a minimum is a high priority for all panel builders. To achieve this, the first requirement is a good design, perhaps one that borrows elements from earlier designs that have been shown to work correctly and efficiently. The next step is accurate documentation for the shop floor, so that the errors are minimised during the building and wiring stages. Good wiring information is particularly important, as a typical control panel will have tens or even hundreds of wires and connections – and one wire incorrectly connected or missing can take a long time to find on test.
End user documentation
Once the project has been completed and is ready to be dispatched, end-user documentation can be easily created with a CAE system, which does all of the hard work. Drawings can be generated at the click of a button, along with parts list, recommended schedules of spares and much else besides. The documentation can be delivered electronically, instead of on paper.
In this blog post we looked at a few key elements of the panel building business model and we described how CAE systems can reduce manual work to a minimum. Getting the right documentation quickly and accurately is a huge benefit in itself. Because at Rittal and EPLAN we provide solutions for all your operational needs, we have put together a comprehensive white paper that will show you how every single element of panel building can be automated or, at the very least, improved.
Click here to sign up and download the paper free of charge:
Comments